L1 Leakage Class
The leakage class is maintained despite very frequent remowal and fastening of panels thanks to the special joining method of panel and profiles. Tight connection between profiles and twin wall panels having 60 mm insulation maintains the L1 leakage class level for many years.
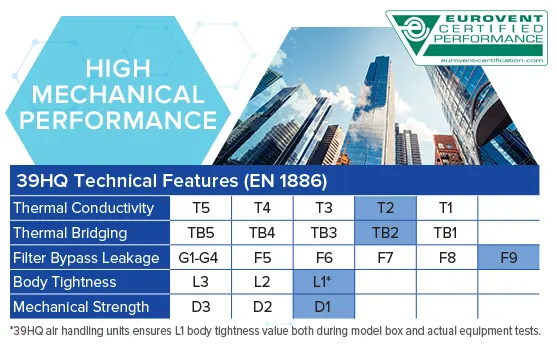
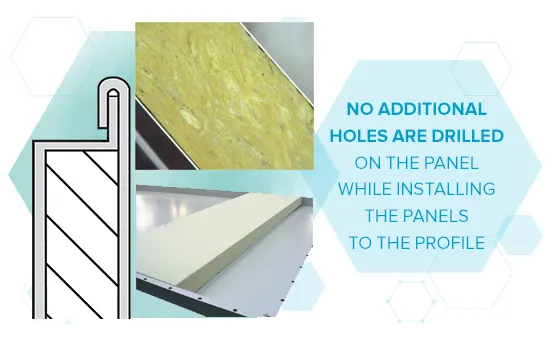
Body
The construction of the Carrier air handling units consists of a profile and panels. Profiled 1-mm thick casing sides of galvanised and coated steel plates ensure a rigid and lightweight frame. The profile holds a 60-mm dual-skin casing wall with panels, doors, inspection hatches and removable centre posts. The casing wall construction comes in several versions of steel plate thicknesses, material types and insulation materials used. The internal plating is always 0.8 mm thick. The standard casing wall construction GP080 consists of 0.8 mm internal and external plating with mineral wool (glass wool) in between.
Profile
Profile is important for the air handling units so much as the skeleton is important for the human body. Polyester powder painted galvanized steel structure with a thickness of 1 mm is used in Carrier 39HQ air handling units. Screw holes are pre-drilled in the supplier and painted afterwards. Density of zinc coating 225 gr/m2 (Z225) Clamped profile structure. Imported from Europe. All side are painted both inside and outside.
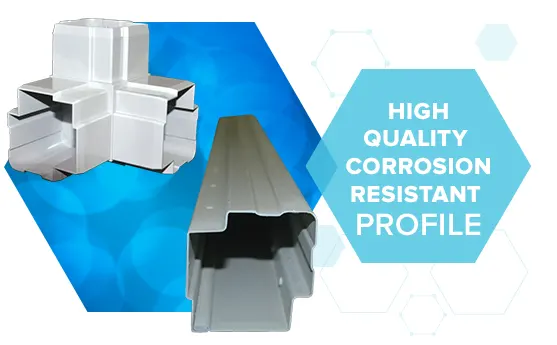
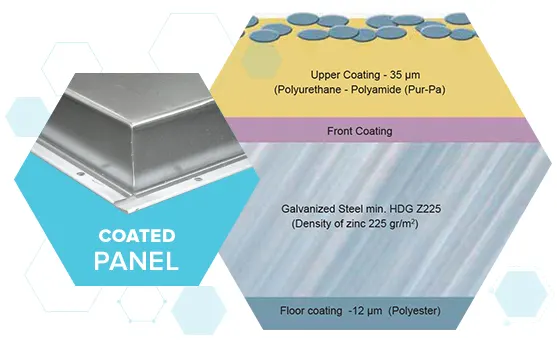
Inner Plate: 0.8 mm
• Galvanized steel (standard) (zinc coating with a density of 225 gr/m2 (Z225))
• Or painted galvanized steel (zinc coating with a density of 225 gr/m2 (Z225))
• Or stainless steel (304 or 316)
Outer Plate: 0.8 mm or 1.25 mm
• Painted galvanized steel (standard) (zinc coating with a density of 225 gr/m2 (Z225))
• or stainless steel (304 or 316) Paint type: Pur-Pa (Polyurethane - Polyamide) powder paint. Resistant against 500 hours of salty water test.
• Colour code RAL 7035
Heat Recovery
Heat recovery systems are used for pre-conditioning the fresh air by using the energy of the exhaust air (by reducing the enthalpy of fresh air in summer time and increasing the enthalpy in winter time). Air thus pre-conditioned shall required less heating/cooling for the required supplying temperature and therefore, energy recovery shall be achieved.
There are many parameters such as initial investment cost, application type, sealing, efficiency, pressure drop, conditions of interior and exterior air, fresh air ratio etc. for the selection of heat recovery type. Heat recovery systems in air handling units are classified into 4 classes.
• Wheel
• Plate
• Run Around
• Heat Pipe
Wheel Type Heat Recovery
Wheel type heat recovery is also classified into three classes as per the heat transfer surface of the heat recovery wheel.
• Condensation
• Enthalpic
• Sorption
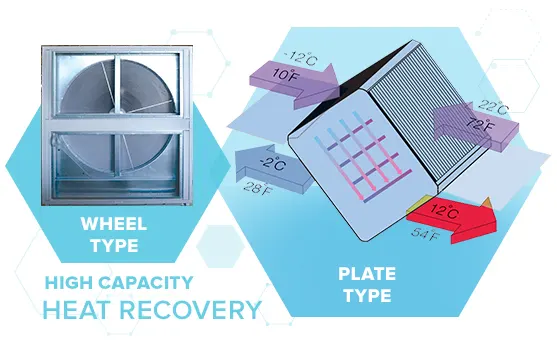
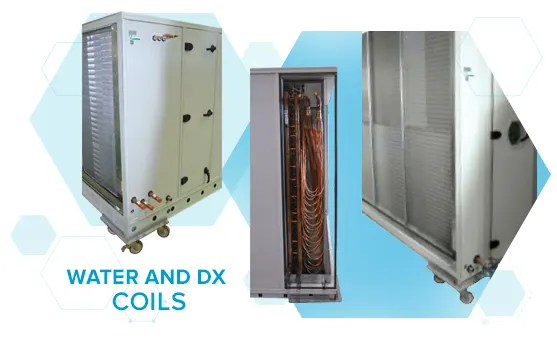
Coils
Heat exchangers used for heating, cooling and/or dehumidifying the air in HVAC systems are usually of the finned pipe type and they are called as coils. Air to be conditioned that flows outside of the finned pipes contact the fin surface. A heating or cooling fluid is circulated inside the pipes. Coils may be hot water coils, cold water coils, DX coils and vapor coils.
As Alarko Carrier, we manufacture the water coils for air handling units and DX coils for rooftop units in our own coil workshop. Besides that, coils can be supplied from other coil manufacturers based on business. All water and DX type coils manufactured are tested with pressurized air test in the water pool inside the factory.
Control
Automatic control system that allows remote management of air handling units used for enhancing the air quality and quality of life in crowded areas such as hospitals, malls, hotels, educational institutions, business centres, banks, public institutions, cultural centres, theatres, airports etc. has also become an integral part of the air handling units. While it is possible to perform positioning or switching, automatic or manual operation of the components of the unit with this system, it is also possible to receive information such as faulty component, operation, dirtiness, freezing etc. Also, this system allows monitoring of measurements such as temperature and humidity, air quality etc. on a Controller with the measurement equipment used. DDC Panel required for SCADA are manufactured as specific for each project with Automated Logic PLC boards with the assurance of Alarko Carrier so that they shall be environment-friendly, safe, light, easy-to-maintain, high quality and warranted. While, a Carrier brand, Automated Logic products are used in 39HQ AHUs.• Provides solutions that offers plug & play operation by leaving the customer the requirement for power supply only,
• Where the procurement, installation and testing of automated control equipments are completed in the factory,
• Where automation software and testing of these software are completed in the factory,
• Where the procurement and installation of MCC-DDC panels on air handling units are completed in the factory,
• Where the procurement and installation of power and control wiring with terminal connections and the procurement and installation of cable spirals are completed in the factory,
• Where ease of installation is provided with special connectors used between the air handling unit modules,
• Where customer is correctly directed about operation and maintenance with the labels used and thus possibility of errors are eliminated.
Control Options:
• Flow Control
• Temperature Control
• Humidity Control
• Differential Pressure Measurement
• Emergency Stop
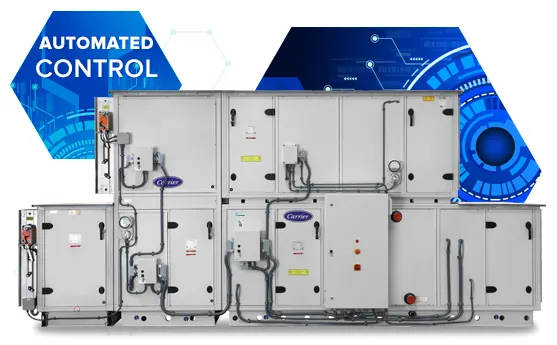
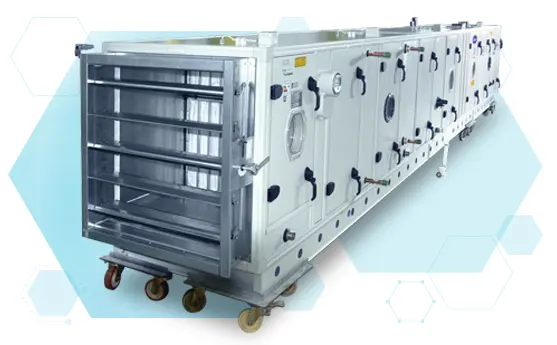
39HQ Hygienic air handling unit has been certified by international accreditation body TUV Sud. These air handling units meet first class sanitary standard high indoor air quality requirements while being used for projects in the health sector. 39HQ Hygienic air handling unit also meets the requirements of EN13053, DIN1964 and VDI6022 standards besides the requirements of EN1886 standard.
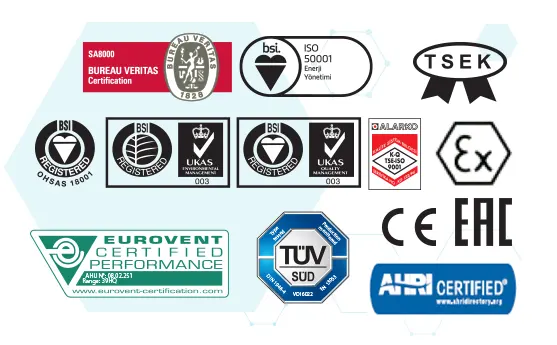